Understanding Die Casting Parts
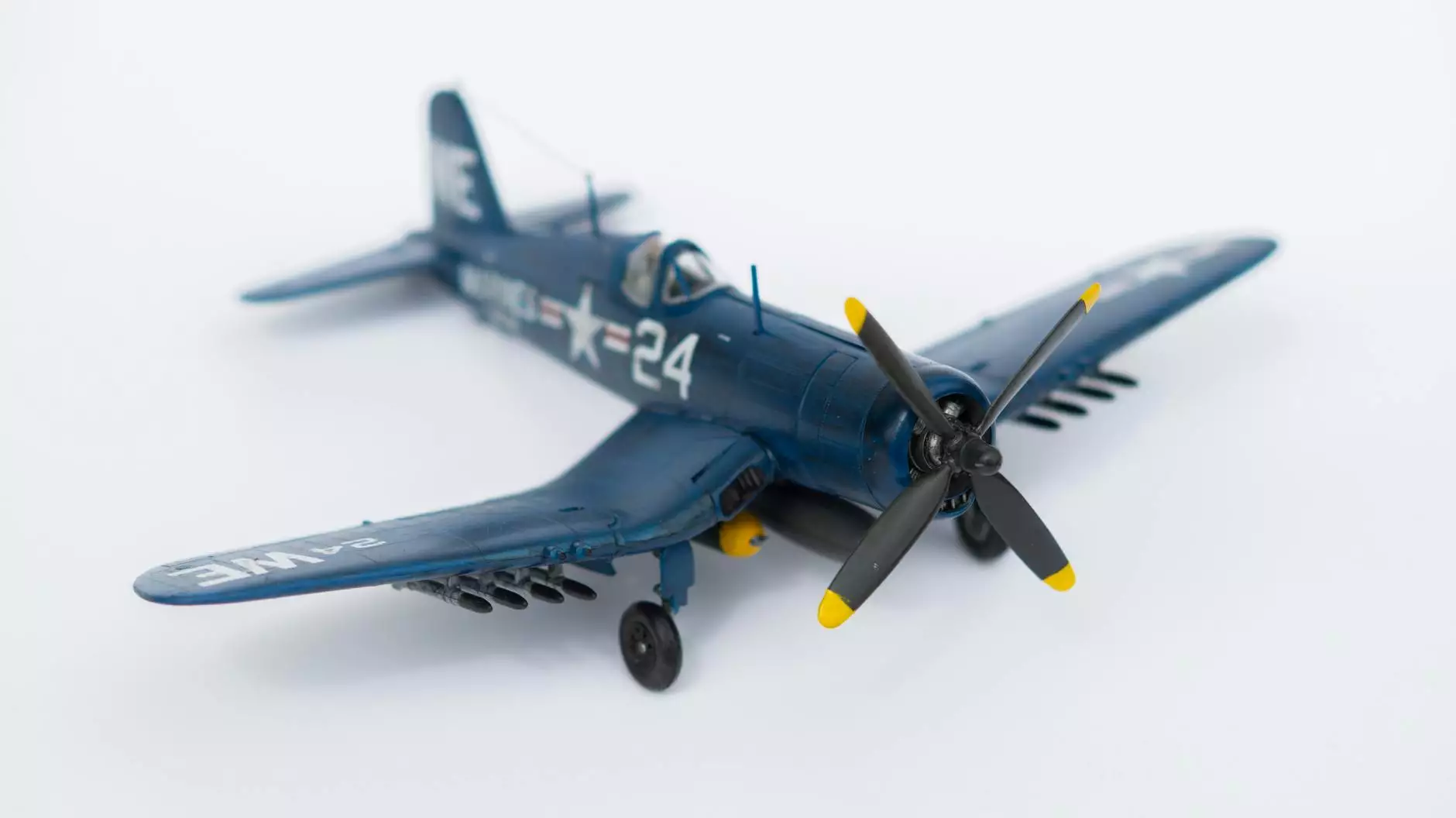
Die casting parts have become integral in a myriad of industries, from automotive to consumer electronics. Understanding the implications and applications of these components is crucial for businesses seeking to enhance efficiency and maintain a competitive edge. This article delves into die casting, its advantages, and its relevance in modern manufacturing practices.
What is Die Casting?
Die casting is a manufacturing process that involves forcing molten metal into a mold cavity under high pressure. This method is particularly suitable for producing complex shapes with high dimensional accuracy and smooth surfaces. The molds, which are typically made from steel, can endure high pressures and temperatures, making them perfect for repeated use.
The Advantages of Die Casting Parts
In the realm of metal fabrication, die casting parts offer several distinct advantages:
- High Precision: Die casting allows for the production of intricate shapes with close tolerances that less advanced processes cannot achieve.
- Cost-Effectiveness: While the initial investment in die casting molds can be high, the ability to produce large volumes of parts efficiently helps reduce per-unit costs significantly.
- Reduced Waste: The die casting process is known for its minimal waste production compared to other manufacturing methods, as virtually all the molten metal that does not enter the die can be reused.
- Versatility: Die casting can be performed using various metals, including aluminum, zinc, and magnesium, allowing for flexibility in selecting materials based on application requirements.
- Excellent Surface Finish: Parts produced through die casting typically require less machining, resulting in improved surface finishes and reduced production time.
The Die Casting Process
The die casting process involves several critical steps, ensuring the production of high-quality die casting parts:
- Mold Preparation: The mold is prepared and aligned to ensure a perfect fit one part to another.
- Metal Heating: The chosen metal alloy is heated until it reaches a molten state, ready for injection.
- Injection: The molten metal is injected into the mold at high speeds and pressure, filling the cavity completely to avoid defects.
- Cooling: Once the mold is filled, the metal cools and solidifies, allowing the production of accurate shapes.
- Extraction: After cooling, the die is opened, and the finished part is ejected, ready for any finishing processes.
Types of Die Casting Processes
There are two primary types of die casting processes: hot chamber die casting and cold chamber die casting. Understanding these variations is essential for businesses looking to optimize their production processes.
Hot Chamber Die Casting
Hot chamber die casting is ideal for metals with low melting points, such as zinc, lead, and tin. In this system, a portion of the melting pot is submerged in molten metal, allowing the die casting machine to maintain a constant supply. This method is known for:
- Increased Efficiency: The continuous feed of molten metal reduces wait times.
- Less Heat Loss: Since the alloy stays in the heating chamber, it experiences less thermal shock.
Cold Chamber Die Casting
Cold chamber die casting is more suitable for high-melting-point metals like aluminum. The process involves pouring molten metal into a cold chamber before injection. This method is characterized by:
- Versatility with Metal Types: Able to handle a wide range of alloys and heat-sensitive materials.
- High Precision Parts: The process is well-suited for applications requiring tight tolerances and intricate designs.
Applications of Die Casting Parts
The versatility of die casting parts makes them beneficial in various industries, including:
- Automotive Industry: Components such as engine blocks, transmission cases, and housings.
- Aerospace: Precision parts for better fuel efficiency and performance.
- Consumer Electronics: Lightweight and durable casings for smartphones and laptops.
- Medical Equipment: Parts requiring stringent quality and performance specifications.
- Appliances: Components like handles, bases, and frames in household devices.
Choosing the Right Die Casting Supplier
When selecting a supplier for your die casting needs, consider the following factors to ensure you collaborate with a reputable and reliable manufacturer:
- Experience and Expertise: Look for manufacturers with a proven track record in die casting and experience in your specific industry.
- Quality Assurance: Ensure they have stringent quality control processes in place to verify the integrity of their die casting parts.
- Technical Capabilities: Assess their capabilities in handling advanced technologies and equipment for custom designs.
- Client Testimonials: Research customer reviews and case studies to gauge the satisfaction of previous clients.
- Cost and Delivery: Compare quotes and examine delivery timelines to find a cost-effective solution that meets your schedule.
Innovation and Future Trends in Die Casting
The die casting industry constantly evolves, driven by technological advancements and consumer demands. Here are some key trends shaping the future of die casting:
- Automation and Robotics: Automated systems streamline production processes, reducing human error and enhancing efficiency.
- Advanced Materials: The use of new alloys, including composites, offers greater strength and lighter weight for die casting parts.
- Sustainability Practices: Manufacturers are increasingly adopting eco-friendly methods, such as recycling scrap metal and minimizing energy consumption.
- 3D Printing Integration: Integration with 3D printing technology allows for rapid prototyping and customization of die casting molds.
Conclusion
In conclusion, die casting parts play a crucial role in the manufacturing sector, providing unparalleled precision, efficiency, and versatility across various industries. As technology continues to advance, the scope of die casting will broaden, enabling businesses to innovate and improve their product offerings. By embracing die casting technology, companies like DeepMould.net can position themselves at the forefront of manufacturing excellence.
Understanding the intricacies of the die casting process, the advantages it offers, and how to effectively select a manufacturer can significantly impact your business success. As industries evolve, staying informed about trends in die casting will prepare you to harness new opportunities and meet the challenges ahead.