Understanding Prototype Injection Molds: The Backbone of Manufacturing Innovation
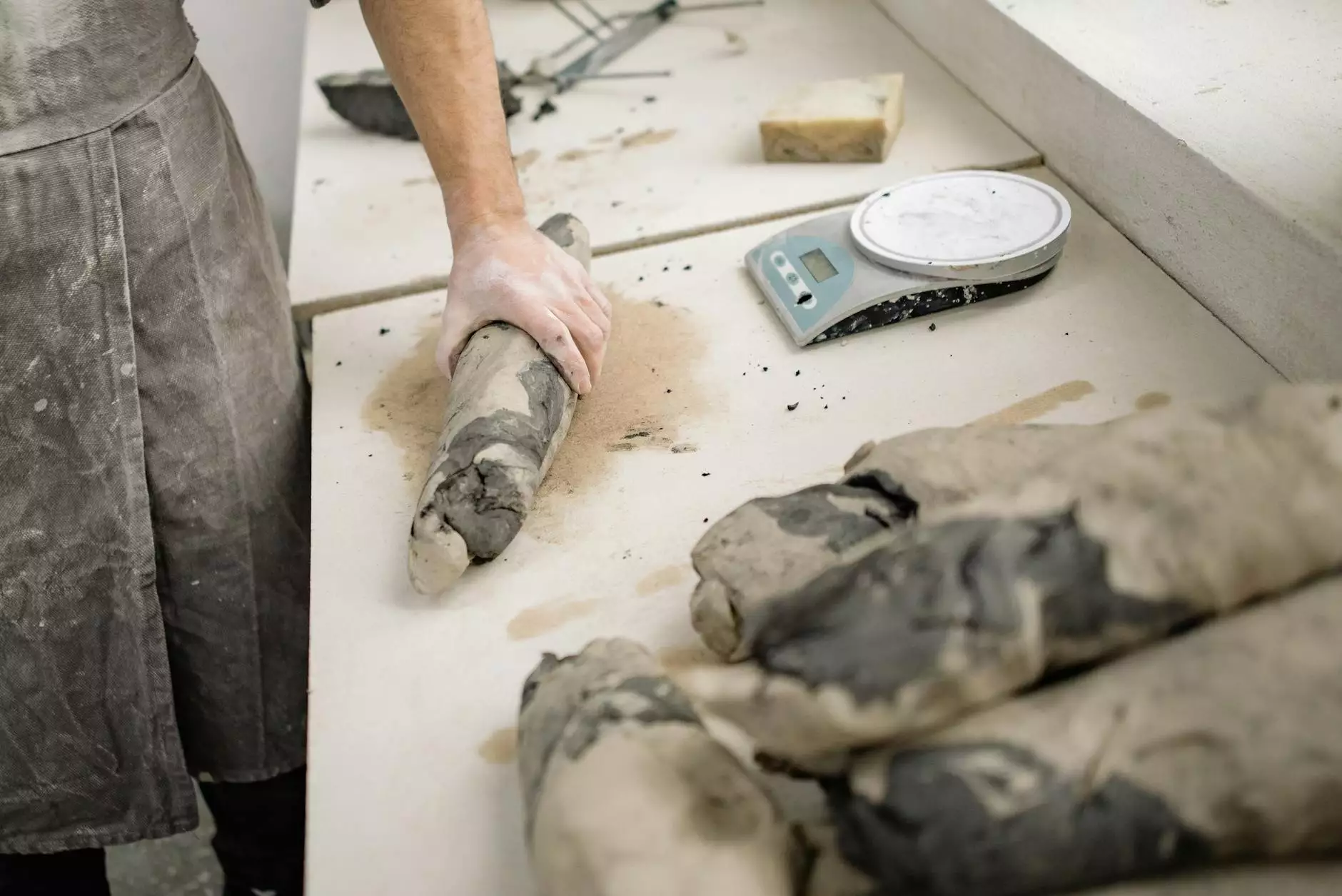
In the ever-evolving world of manufacturing, staying ahead requires not just the right tools but also the right techniques. One such technique that has transformed product development is the use of prototype injection molds. These molds are pivotal in proving concepts, shortening development timelines, and enhancing product quality across various sectors, particularly in metal fabrication. This article dives deep into the intricacies of prototype injection molds, their importance, and their applications in the manufacturing world.
What are Prototype Injection Molds?
Prototype injection molds are specialized tooling designs that enable manufacturers to produce components in a way that closely resembles the final production models. This process involves injecting molten material into the mold to create a desired shape, allowing for the rapid production of test items in a variety of materials, including metals, plastics, and composites. The primary purpose of these prototypes is to facilitate testing, validation, and iterative design adjustments before full-scale production begins.
The Process of Creating Prototype Injection Molds
The creation of prototype injection molds involves several well-defined stages, each critical to the overall success of the project. These stages include:
- Initial Concept and Design: This phase begins with a thorough discussion concerning the product requirements and specifications, followed by the development of a digital 3D model using CAD software.
- Material Selection: Choosing the right materials for the mold and prototype is crucial. Metal fabricators often choose high-grade steel or aluminum for durability and thermal conductivity.
- Mold Fabrication: Once the design is finalized, the mold is manufactured using precision machining techniques, ensuring tight tolerances and high-quality finishes.
- Injection and Testing: The molten material is injected into the mold, allowed to cool, and then extracted. The resulting prototypes are then subjected to various tests to assess functionality and aesthetics.
- Iterative Refinement: Feedback from testing may require adjustments to the prototype, necessitating redesign and re-production, thus ensuring that the final product meets all specifications.
Advantages of Using Prototype Injection Molds
Utilizing prototype injection molds in the manufacturing process offers numerous advantages, including:
- Cost Efficiency: While initial mold-making can be expensive, the overall costs often reduce by eliminating the need for extensive revisions during later production stages.
- Faster Time-to-Market: Prototyping allows manufacturers to quickly test and iterate designs, significantly hastening the development cycle.
- Improved Product Quality: With the ability to test and refine prototypes, companies can ensure higher quality in the final product, reducing failures in the field.
- Greater Design Flexibility: Prototype molds enable designers to explore diverse solutions and modifications in a fraction of the time required for traditional methods.
- Enhanced Collaboration: The tangible nature of prototypes facilitates better communication between teams and clients, fostering collaboration in refinement and product finalization.
Applications of Prototype Injection Molds in Metal Fabrication
In the realm of metal fabrication, the role of prototype injection molds cannot be overstated. They serve as an essential tool across various applications:
1. Automotive Industry
The automotive sector relies heavily on precise and efficient prototyping to test parts such as dashboards, panels, and other intricate components. Prototype injection molds allow for the rapid production of these parts to ensure they meet safety standards and performance requirements.
2. Consumer Electronics
The fast-paced nature of the electronics industry means that design iterations occur rapidly. Prototype injection molds enable companies to produce cases and components for testing how they fit and function, leading to better designs and shorter development times.
3. Medical Devices
In the medical field, precision is imperative. Prototype injection molds allow manufacturers to create device prototypes that meet strict regulatory standards. Testing prototypes aids compliance with health and safety standards while ensuring functional efficacy.
4. Industrial Components
Prototype molds aid in developing various industrial tools and components, providing businesses with insights into design and function that can help in optimizing operational workflows.
Choosing the Right Partner for Prototype Injection Molds
Selecting the right manufacturing partner for prototype injection molds is critical. Here are several factors to consider:
- Experience and Expertise: Look for companies with a proven track record in metal fabrication and prototyping, such as DeepMould.net.
- Technology and Equipment: Ensure that your partner uses state-of-the-art technology and equipment to optimize the quality of the molds produced.
- Quality Control Processes: A rigorous quality control process is essential to ensure that prototypes meet required standards before testing.
- Customization Capabilities: The ability to tailor molds to unique specifications can significantly impact project outcomes.
- Support and Communication: Good communication channels and responsive support are invaluable throughout the prototyping process.
The Future of Prototype Injection Molds
As technology advances, so too do the capabilities of prototype injection molds. Innovations such as 3D printing and advanced materials are set to revolutionize the prototyping landscape by allowing even quicker turnarounds, reduced costs, and greater flexibility in design.
Emerging Trends
The following trends are expected to shape the future of prototype injection molds:
- Integration of Smart Technology: The incorporation of IoT devices in the mold manufacturing process can lead to improved monitoring and optimization of production conditions.
- Biodegradable Materials: As sustainability becomes a focus, using eco-friendly materials for prototypes can attract environmentally conscious consumers.
- Automation: The rise of automation in manufacturing can streamline the molding process, reducing lead times and increasing accuracy.
Conclusion
In summary, prototype injection molds serve as a critical component in the development and manufacturing of various products across several industries. By facilitating quick iterations, improving product quality, and reducing costs, these molds allow businesses to maintain a competitive edge. As trends continue to evolve, companies that leverage the advantages of prototype injection molds are poised to thrive in an increasingly demanding marketplace.
For metal fabricators, understanding and utilizing prototype injection molds is not just advantageous; it's essential for success. Ensuring that you partner with a skilled and experienced provider will influence not only the quality of your prototypes but the overall productivity of your manufacturing processes. Explore your options today and unlock the potential of your manufacturing capabilities!