Understanding Plastic Injection Mold Shops: A Comprehensive Guide
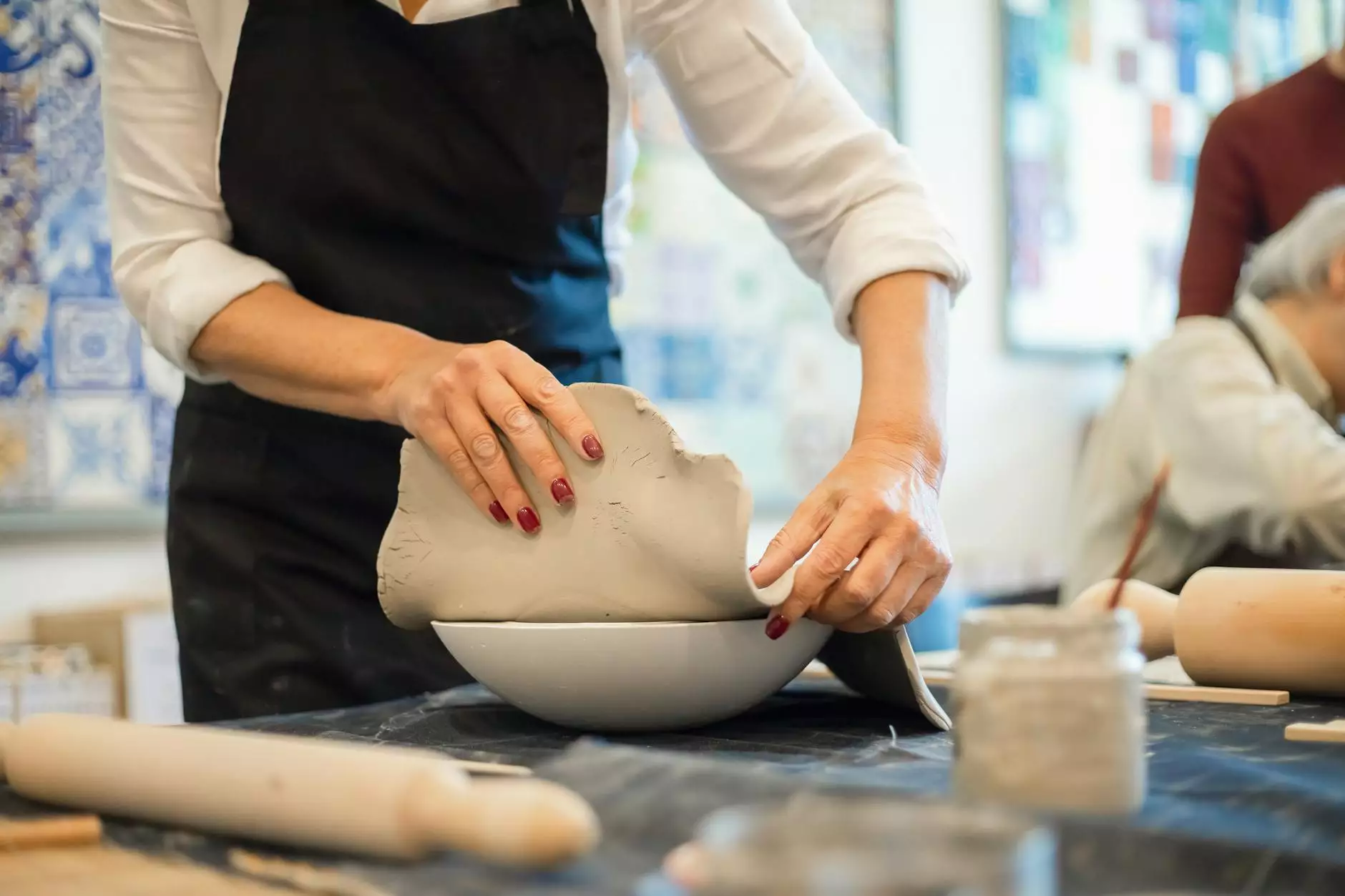
Introduction to Plastic Injection Mold Shops
Plastic injection mold shops are essential entities in the manufacturing sector, specializing in creating high-quality plastic parts through a highly efficient process. This article delves into the workings of these shops, the process of injection molding, their significance in various industries, and the future of this technology.
What is Plastic Injection Molding?
Plastic injection molding is a manufacturing process that involves injecting molten plastic into a mold to create specific shapes and designs. This process has revolutionized the way products are manufactured by allowing for high-volume production of precision parts. Here’s a closer look at how it works:
- Material Selection: The process begins with the selection of high-quality thermoplastics or thermosetting materials suited for the desired product.
- Mold Design: The mold must be designed with precision to ensure that it can withstand the pressure of injected plastic and create the desired shape.
- Melting the Plastic: Pellets of plastic are fed into a heated barrel, where they are melted and mixed properly.
- Injection Process: The molten plastic is injected into the mold cavity under high pressure, ensuring the material fills every intricate detail.
- Cooling: Once injected, the plastic is allowed to cool and solidify while still in the mold.
- Demolding: After cooling, the mold is opened, and the newly formed plastic part is ejected.
Key Components of Plastic Injection Mold Shops
Plastic injection mold shops are equipped with various tools and machinery that are vital for the injection molding process. Some of the key components include:
- Injection Molding Machines: These machines are the heart of the operation, where the molten plastic is injected into molds.
- Molds: Precision-engineered molds are essential for achieving the desired specifications and surface finishes.
- Auxiliary Equipment: This includes temperature control units, granulators, and robots that enhance the efficiency of the injection molding operation.
- Quality Control Equipment: Ensuring that the final products meet strict standards is crucial, and advanced quality control tools are employed.
Advantages of Using Plastic Injection Mold Shops
Working with established plastic injection mold shops comes with several advantages:
- High Efficiency: Injection molding is one of the most efficient manufacturing processes, allowing for rapid production of large volumes of parts.
- Precision and Consistency: The injection molding process ensures that identical parts are produced with exceptional precision, minimizing the variability seen in other manufacturing methods.
- Cost-Effective: While initial setup costs can be high, the long-term savings in production make injection molding a cost-effective solution for mass production.
- Design Flexibility: Modern mold design techniques allow for complex geometries that would be impossible with traditional manufacturing methods.
Applications of Plastic Injection Molding
The versatility of injection molding leads to its usage in various sectors. Some of the primary industries benefiting from this technology include:
- Automotive Industry: From dashboards to bumpers, plastic parts are extensively used in automobiles, enhancing performance while reducing weight.
- Consumer Products: Household items, toys, and packaging solutions are often manufactured using injection molding techniques.
- Medical Devices: The medical industry requires precision-made components that meet strict regulations, and injection molding provides that.
- Electronics: Injection molded parts are integral in casing and components for various electronic devices.
Choosing the Right Plastic Injection Mold Shop
When selecting a plastic injection mold shop, several factors should be considered to ensure you are partnering with a capable provider:
- Experience and Expertise: Look for shops with a proven track record and specific experience relevant to your industry.
- Quality Assurance Processes: Ensure they have robust quality control measures to maintain high standards in production.
- Technology and Equipment: The latest technology will ensure efficiency and precision in manufacturing.
- Customer Support: A supplier that offers excellent communication and support throughout the project will enhance your overall experience.
The Future of Plastic Injection Mold Shops
With advancements in technology, such as automation and 3D printing, the future of plastic injection mold shops looks promising. Here are some trends that are shaping the industry:
- Increased Automation: Automation is reducing labor costs and improving efficiency, allowing for quicker turnaround times.
- Integration of Industry 4.0: The incorporation of IoT (Internet of Things) in manufacturing is enhancing real-time monitoring and predictive maintenance.
- Material Innovation: Continuous development in biodegradable and recyclable materials is making injection molding more sustainable.
- Customized Solutions: The demand for tailor-made parts is increasing, and shops are adapting by offering bespoke services.
Conclusion: The Vital Role of Plastic Injection Mold Shops
In summary, plastic injection mold shops are a cornerstone of modern manufacturing, providing a range of industries with efficient, high-quality, and cost-effective solutions. As technology continues to evolve, these shops are poised to adapt and innovate, further solidifying their importance in the manufacturing process. By understanding their capabilities and advantages, businesses can make informed decisions and leverage plastic injection molding to enhance their production capabilities.
For more information on how Deep Mould can assist with your injection molding needs, visit our website at deepmould.net.